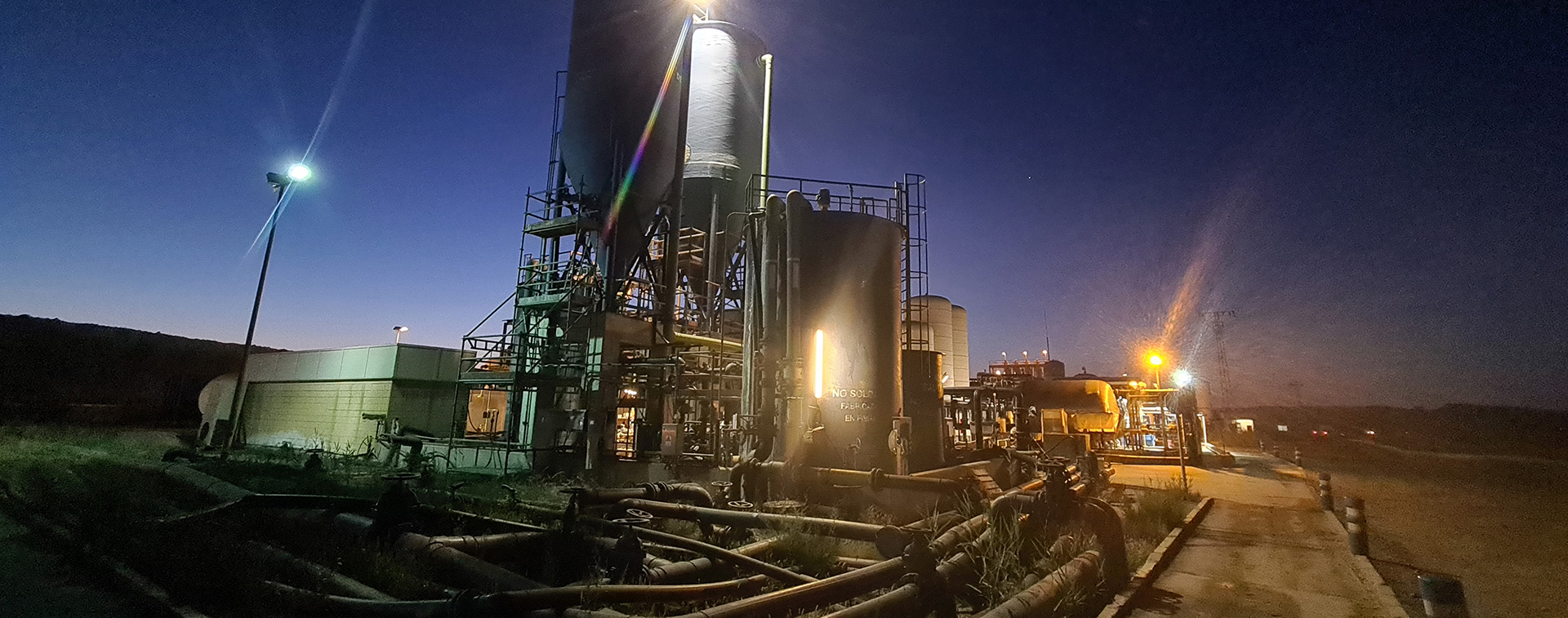
- Type of work:
- Industrial water
- Clients:
- Cobre las Cruces (First Quamtum Mining)
- Location:
- Spain
Water treatment plants of the Las Cruces Copper Mining Complex. Construction, upgrading and operation (Seville)
Lantania carried out the construction of the Permanent Water Treatment Plant (PWTP) in 2010 and since 2023 it is in charge of executing phase I of the expansion of said facility to adapt it to the increase in needs associated with the PMR (Poly Metallurgical Refiniery) project. The construction project model for these works has been based on Building Information Modeling (BIM) to optimize planning, coordination, and execution of the works. Likewise, Lantania currently has a contract for the operation service of the water plants and facilities within the Cobre las Cruces mining complex in Gerena (Seville), which consist of:
• Treatment plant for water from the exploitation fronts and dumps, with a capacity of 200 m3/h. This flow will be treated to be used either as process water in the hydrometallurgy plant, with a quality limited by a chloride concentration of less than 30 ppm, or for reinjection into the aquifer, guaranteeing a 90% water recovery yield.
Consists of:
- Three ultrafiltration lines.
- Three lines of reverse osmosis with spiral membranes with three stages.
- Four reject recovery units with flat membrane technology and one unit with spiral membranes, all with two stages.
The upgrading consists of increasing the pre-treatment flow from 200 m3/h to 385 m3/h thanks to the construction of a lamella type decanter to treat 185 m3/h. After this, a new filtration system will be built for a flow rate of 400 m3/h with a glass + anthracite filter bed in vertical GRP bottles and a bed cleaning system by backwashing with water.
The extra ultrafiltration design flow is increased by 200 m3/h through ultrafiltration modules with Multibore membranes (dizzer® XL), “inside-out” filtration model.
The reverse osmosis design flow is increased by 180 m3/h through a reverse osmosis line with three stages.
• Water treatment plant for the drainage and reinjection system from the aquifer above the mineral extraction line, 750 m3/h. This water, once treated, will be reinjected into the aquifer, guaranteeing a minimum yield of 90% and a quality below the injection threshold values according to types and location, equivalent to drinking water.
Consists of:
- Three ultrafiltration lines
- Three reverse osmosis lines with three stages
The upgrading consists of the use of existing flint filters in the current contact water treatment plant (the system consists of four horizontal GRP filters of diameter= 3 m and length= 5 m) changing the filter bed from flint to glass + anthracite.
• High recovery plant for the treatment plant for concentrates from the reverse osmosis system and the drainage and re-injection system, 50 m3/h, consisting of:
- Lamellar decanter.
- Press filter.
- Ultrafiltration.
- 1-stage reverse osmosis.
• Forced evaporation plant for concentrates from the high recovery system, 14 m3/h, consisting of a six-effect evaporator.
• Systems of rafts, tanks and pumping from points of origin within the mine to its impulsion for reinjection into the aquifer or reuse in the hydrometallurgical plant for copper production.
Additionally, Lantania operates the following auxiliary facilities:
• Process water production plant, in charge of generating quality water for the hydrometallurgical process from contact water or water from the discharge of the North WWTP – Seville. It consists of a lamellar decanter and sand filters with a treatment capacity of 150 m3/h.
• Plant for conditioning water from the WWTP for reinjection into the aquifer with a capacity to produce 200 m3/h. For this, a treatment line is used consisting of hyperchlorination, sand filtration and ultrafiltration.
• Two-stage reverse osmosis plant for the production of high-quality water (chlorides < 10 ppm) and a capacity of 40 m3/h.
• Water treatment plant for 40 m3/d.
• Supply lines from WWTP Norte-Seville and discharge line.
The operation and maintenance team is made up of 40 workers.
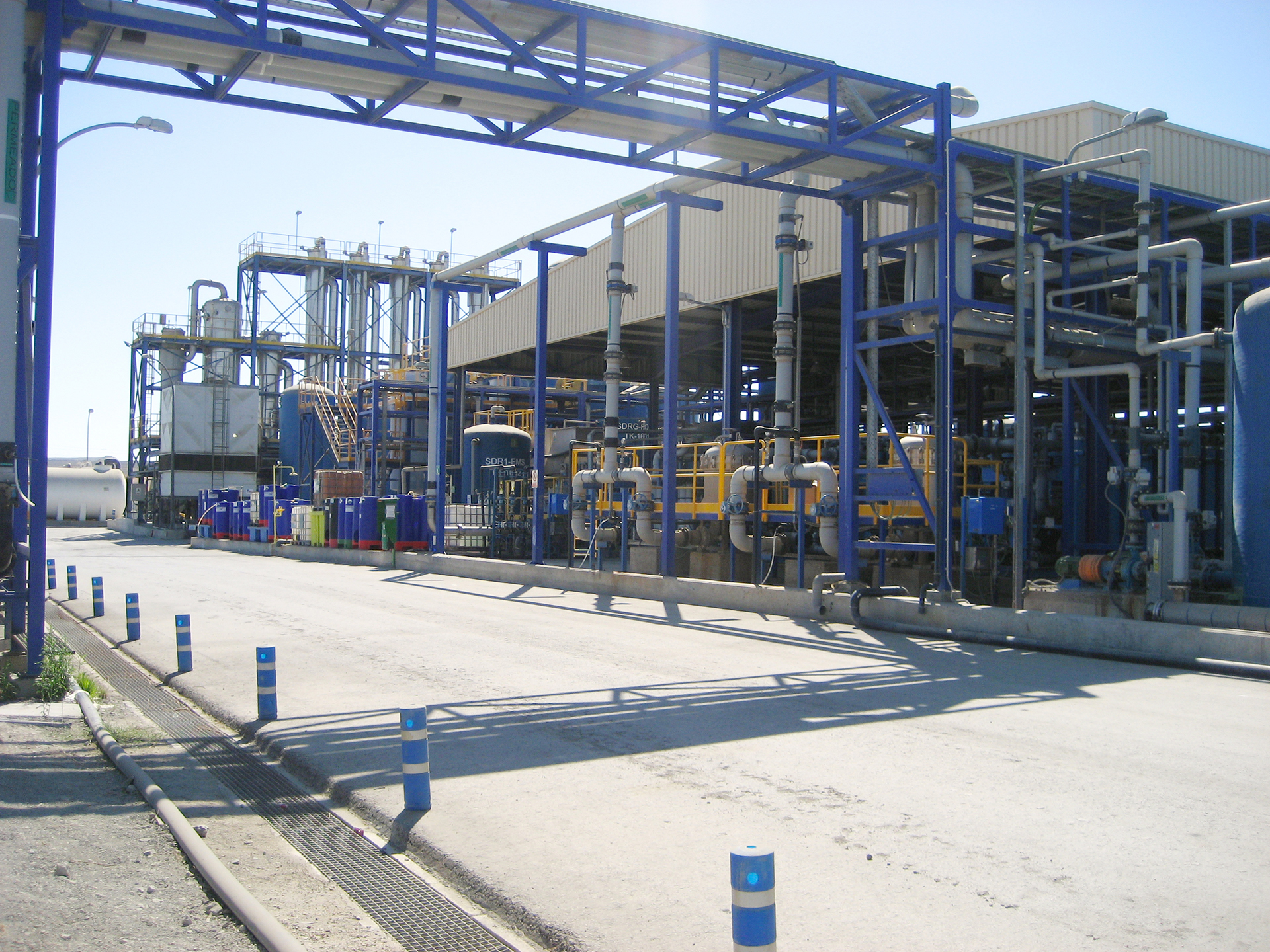